Your reliable source for quality complex composite part design, engineering, fabrication and assembly for a range of industrial and aerospace applications.

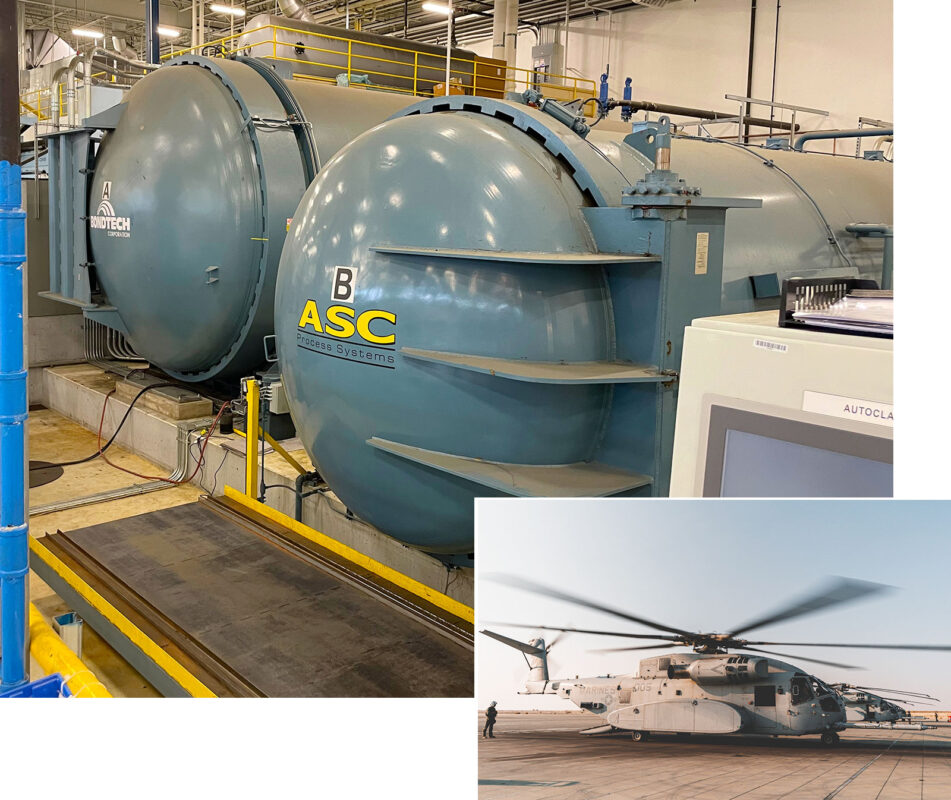
An Innovative Partner Delivering Reliable Complex Composite Parts
When you’re looking for a composite manufacturing supplier, you need a partner you trust to deliver consistent quality, innovative solutions and a competitive price. TIGHITCO has been providing build-to-print industrial and aerospace composite manufacturing services for customers around the world for more than 50 years.
- Excellent ResponsivenessTIGHITCO's team is excellent on responsiveness and working with their customers to ensure open items are resolved and parts are delivered. The program, sales, engineering, quality, and operations teams are always willing to work with us and ensure parts delivered in a timely manner.
Industries We Serve

Complex Composites Manufacturing & Assembly Capabilities
Composites Fabrication & Assembly
Design & Engineering
Non-Destructive Testing & Inspection Capabilities
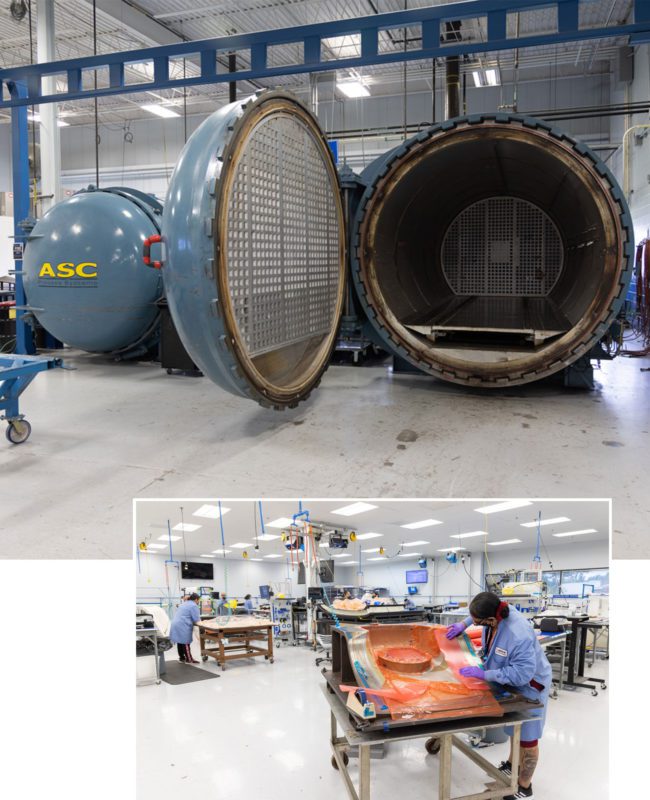
Your Partner for Advanced Composites & Production
With decades of experience in composite aerostructure engineering, fabrication and assembly, TIGHITCO has the expertise and the equipment to develop solutions to your most challenging applications. Our expertise goes beyond the aviation industry to deliver quality complex composites for the industrial, space and energy sectors, among others. We have the capacity to handle large parts and our Six Sigma lean manufacturing processes help us deliver efficient, cost-effective composite manufacturing services for your application. You can count on us for rapid response and warranty-backed products with efficient post-production support. And with five locations across the U.S. and Mexico, we can deliver the most cost-effective production for your needs.
Our Composite Fabrication Equipment
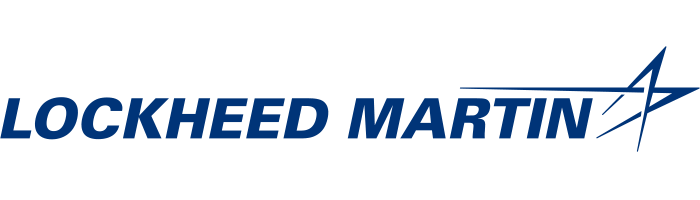
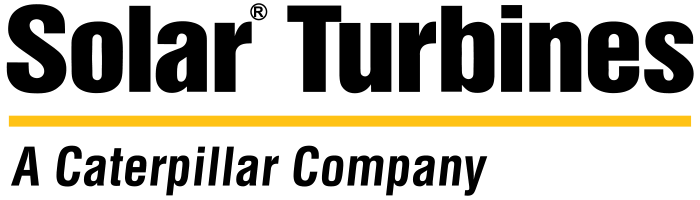
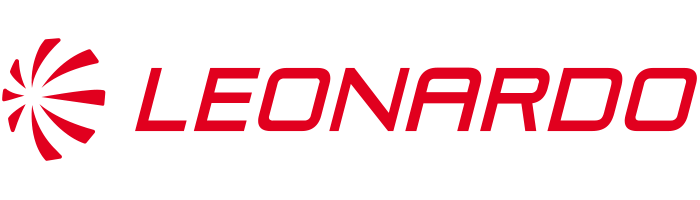
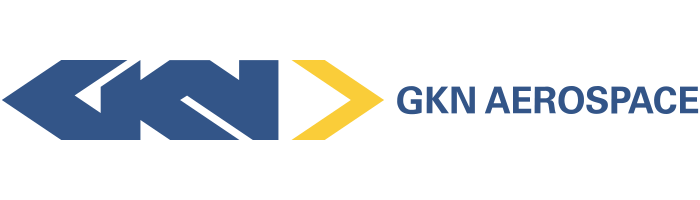
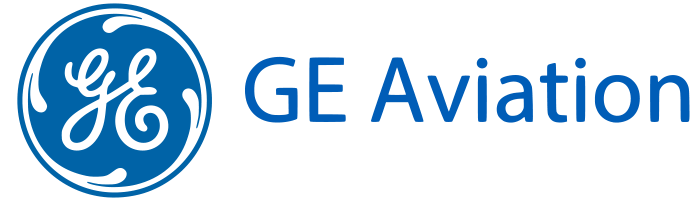
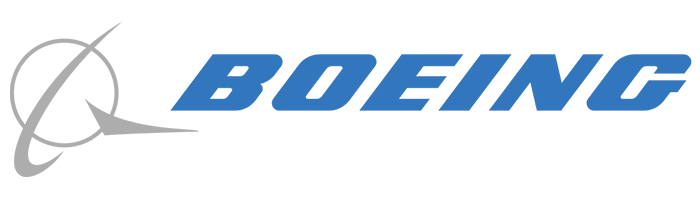
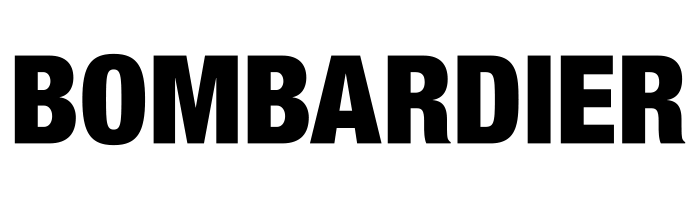
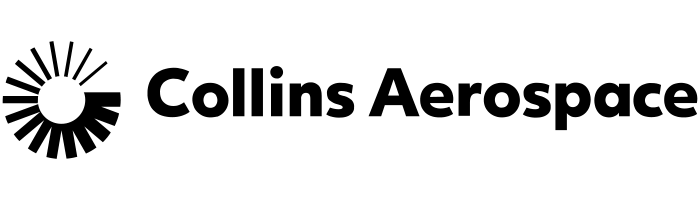
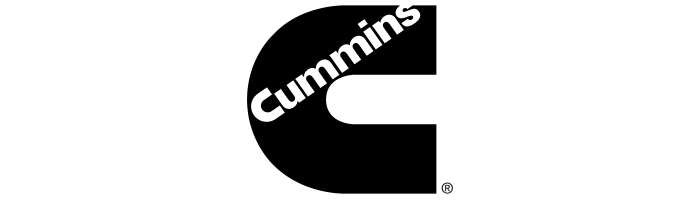
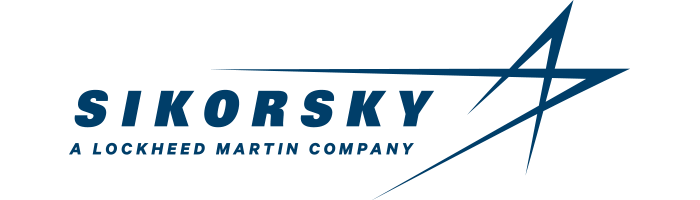
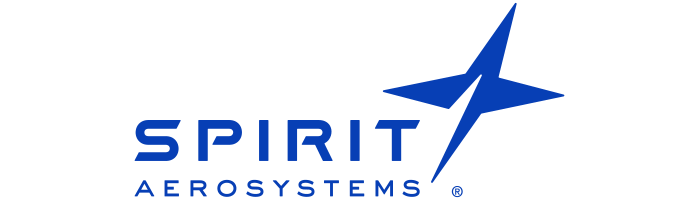
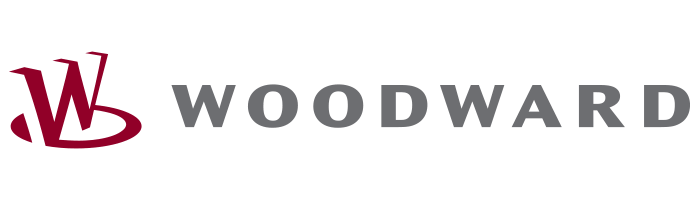
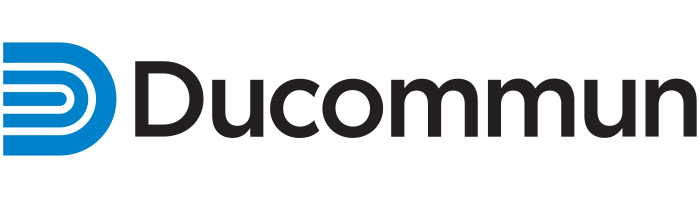
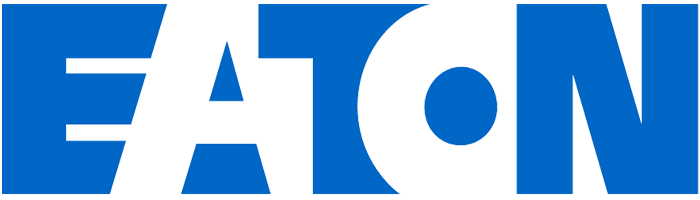
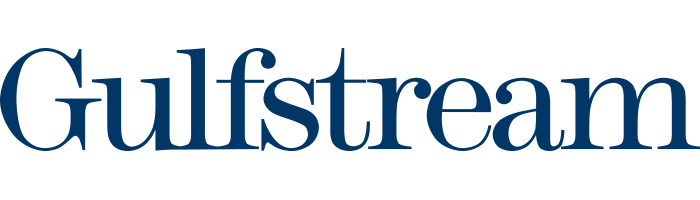
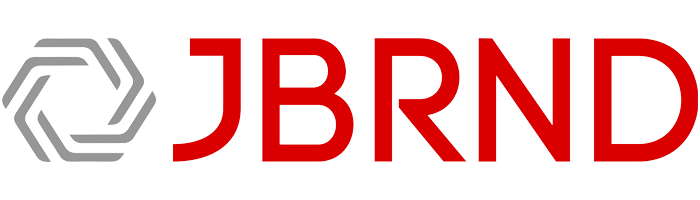
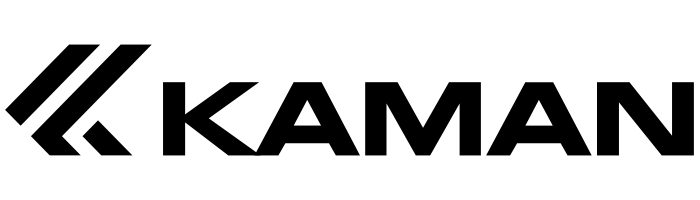
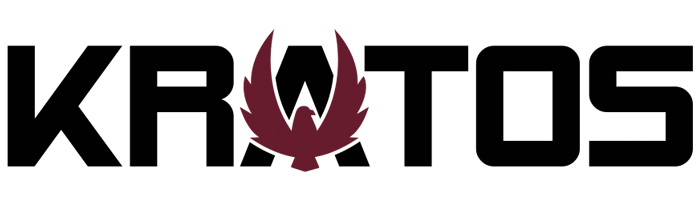
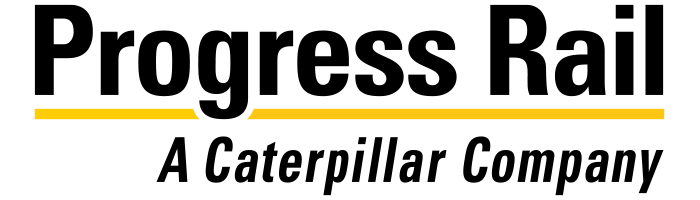
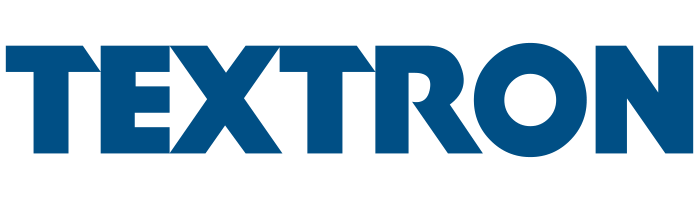
Our Composite Engineering Process
Certification Support
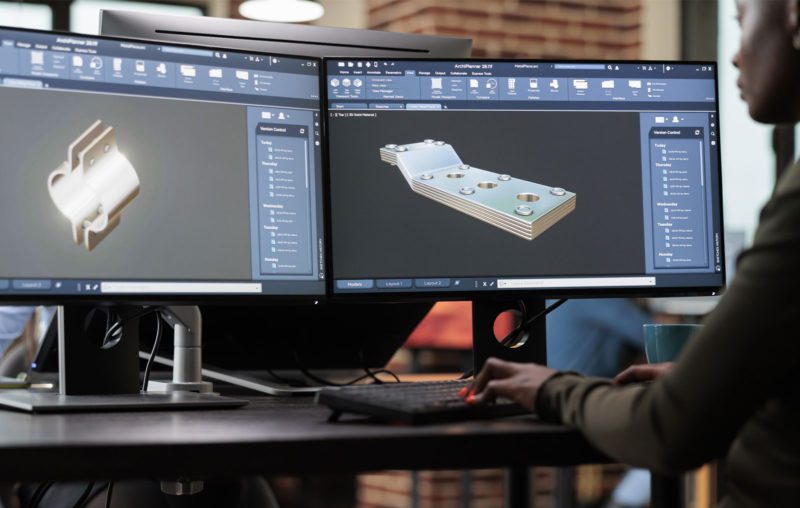
Composite Part Design
Manufacturing Planning
Aircraft Composite Repairs
Abrasions and punctures: Minor surface damage like scratches and dents.
Disbonding and delamination: Separation of skin from core, often caused by impact.
Water damage: Water seeping into cracks, potentially causing structural issues.
Fuel damage: Contamination from fuel, oil, or hydraulic fluid, often requiring material replacement.
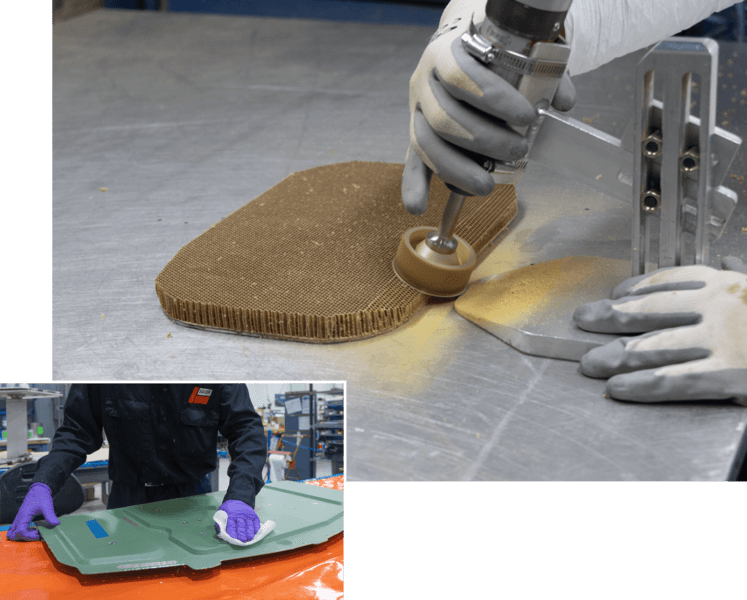
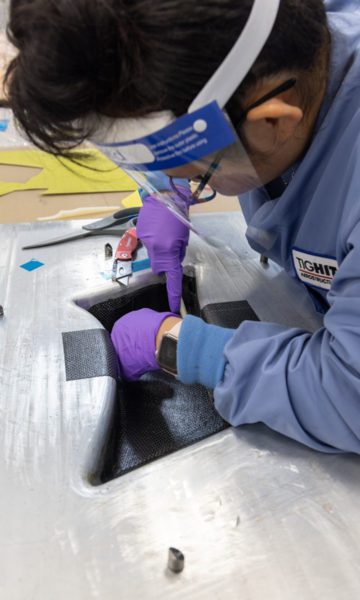
Composite Repair Process
1. Disassemble, Clean, and Inspect:
Thoroughly assess the damage using visual inspection and specialized techniques like:
- Non-destructive inspection (NDE)
- Paint removal
- Tap testing
- Ultrasound
Follow OEM guidelines specific to the material, part, and brand.
2. Composite Repair and Overhaul:
Repair type depends on the severity and type of damage:
- Nonstructural Repairs: Cosmetic fixes like adding filler, sanding, and repainting.
- Semi-structural Repairs: Address more than cosmetic damage, involving core material removal and rebuilding with laminates.
- Resin Injection Repairs: Temporary fix for delamination by injecting resin.
- Structural Repairs: Extensive repairs to primary structural parts using methods like scarfing or stepping to restore original strength and stiffness.
3. Assemble and Test:
Reassemble components and conduct thorough inspections or tests per OEM criteria. Ensure proper curing, bonding, and absence of porosity or voids in the repair before returning the part.